Responsible
Leadership
New Balance builds global brands that athletes are proud to wear, associates are proud to create and communities are proud to host.
Product
The New Balance story is rooted in product innovation around the concept of balance and a chicken’s foot. Today, we are challenging convention to advance the sustainability of our products in materials and design, product chemistry and packaging.
New Balance’s green leaf standard
New Balance’s green leaf standard indicates environmentally preferred material adoption across our footwear and apparel products. For apparel that meet New Balance’s green leaf standard, at least 50% of the materials in a garment are sourced as environmentally preferred. For footwear that meets New Balance’s green leaf standard, at least 50% of the materials in its upper are sourced as environmentally preferred, and at least one material in the midsole/outsole uses approximately 3% bio based or 5% recycled content. We call a material environmentally preferred based on its physical characteristics (for example, recycled polyester) or based on its more sustainable sourcing practices (for example, Better Cotton).
Precise details of how a product meets the green leaf standard can be found on a garment’s care label, footwear or garment hangtag, or the product listing on www.newbalance.com.
USING MORE ENVIRONMENTALLY PREFERRED MATERIALS
Choosing more environmentally preferred fibers and materials is one of the best and most immediate ways we can reduce our impacts. We are focused on transitioning our three most highly used materials—polyester, leather and cotton – to environmentally preferred options. By 2025, our goal is for all our cotton and leather to be from preferred sources and 50% of our polyester to be recycled.
We’re just getting started and realize this is not enough. Sustainable materials are continuously evolving, and we continue to find new answers and make even better decisions. We’d love to hear from you. Please send us a note and tell us what else you would like to see or what else you expect from us as a responsible brand.
Recycled Polyester
Polyester is our most highly used fiber and is an incredibly flexible and adaptable material. But, polyester is made from fossil fuels and requires intensive processing to be turned into useful materials for footwear and apparel. Recycled polyester is made from recycling plastic waste into new fibers and yarns. Using recycled polyester reduces our reliance on new fossil fuels, requires less energy and water, and diverts plastic waste that would otherwise pollute our land, water and air for years to come. This approach does not completely solve our reliance on polyester but is a first step to set us on the right track. We are accelerating this transition by focusing on polyester materials we use the most – some of which are very visible to you and others that make up inner linings and other internal components.
Organic Cotton
Cotton is among our top three textiles – a natural fiber that has been used for thousands of years. Cotton farming, however, requires vast amounts of water and chemicals. Organic cotton is grown and processed according to standards that avoid the use of persistent toxic chemicals and maintain local soil health and biodiversity. This is better for the environment and farmers. We consider organic cotton to be preferred, and we continue to evaluate other options as well. Any organic cotton currently used is certified according to Global Organic Textile Standards (GOTS).
Preferred Leather
Leather can offer unparalleled craft, comfort, quality, fit and durability, but the production of natural leather can result in significant environmental impacts throughout the supply chain, from farm to tannery. We define preferred leather in two ways: leather that comes from LWG Gold-rated tanneries or chrome-free leather. Our goal is for 100% of our leather to meet at least one of these two criteria by 2025. We are also investigating and prototyping various leather alternatives.
LWG Gold: The Leather Working Group (LWG) audits and certifies tanneries based on their ability to demonstrate good environmental practices in all aspects of leather production. We currently source leather primarily from Silver and Gold tanneries, and we consider leather from Gold tanneries to be “preferred.” More information on the Leather Working Group can be found at www.leatherworkinggroup.com.
Chrome-free leather: Most leather is tanned with a chemical called Chromium III, which can undergo changes and become harmful to people and the environment when leather is disposed. Chrome-free leather uses different chemicals during the tanning process, eliminating chromium from the production process.
TENCELtm
Lyocell is a fiber made from wood pulp and offers an alternative to cotton. TENCELtm by Lenzing is a lyocell fiber derived from sustainably sourced wood pulp and specifically produced in a closed loop process, meaning they recycle water and reuse non-toxic solvents. When compared to cotton, TENCEL requires less energy and water than cotton production and does not require use of pesticides and insecticides.
Besides these criteria, all of our leather also meets our broader Animal Materials Policy that defines requirements for sourcing animal materials and ensuring animal welfare is protected and that exotic skins are not used in our products. Our Animal Materials Policy can be found in our Restricted Substances Manual.
Surplus Materials
One way to be more sustainable is to use surplus materials that already exist. Surplus material refers to old unused materials that are left over from production – we may have ordered too much, or the color could have been wrong. There are many things that can lead to surplus materials. We are working to reduce the creation of excess materials while finding ways to use the surplus material that we have on hand.
Preferred Soles
Most of our sole materials are made out of EVA or rubber. EVA foam provides unparalleled cushioning, but a primary ingredient in EVA is derived from petroleum. While natural and synthetic rubber outsoles provide durability and traction, natural rubber has been connected to deforestation, and synthetic rubber is derived from petroleum.
EVA: We are making small changes that go a long way with our EVA compounds. We have selected our most used EVA compounds, and we are replacing approximately 3% of each formulation with a sugarcane based foam compound starting with shoes launching in 2022. Sugarcane is a renewable resource and will start to help us reduce our reliance on petroleum. We only source sugarcane that does not compete with local food sources. By applying this seemingly small change across our most used EVA compounds, we are making a huge change at the brand level. We implemented these new compounds on over 20% of shoes in our spring 2022 launch.
Rubber: For many of our most used outsole materials, we are incorporating approximately 5% reprocessed rubber waste back into our rubber formulations starting with shoes launching in 2022. This small change helps to lessen a waste stream and reduce our reliance on virgin materials. We implemented these new formulations on over 14% of shoes that we introduced in our spring 2022 launch.
INDUSTRY COLLABORATION
New Balance is proud to work with leading organizations in the apparel and footwear industry to advance product sustainability and preferred materials. These relationships help us leverage common tools, open pathways to important research, and provide opportunities to work on collaborative solutions that can help improve conditions across the entire industry. We are active members of:
• Textile Exchange (TE)
• Outdoor Industry Association (OIA)
• Leather Working Group (LWG)
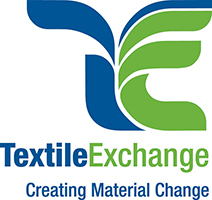
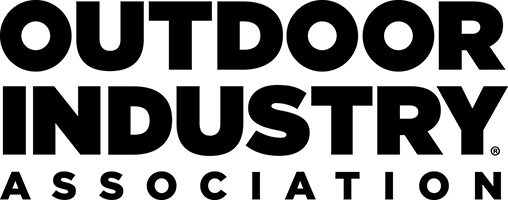
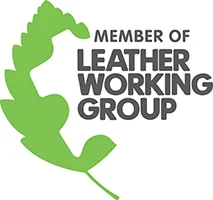
We are also working with our suppliers to develop innovative new materials and find new ways to use manufacturing waste. Many of our material suppliers have already created closed loops within at least a portion of their manufacturing process. More than half of our strategic footwear and apparel suppliers have reported incorporating at least some pre-consumer scrap back into making new materials, either at their own facilities or at a nearby site. Nearly 20% say they reincorporate most or all of their manufacturing scrap. And nearly 40% offer a takeback program to close the loop between Tier One and Tier Two suppliers.
LONGEVITY
Current patterns of consumption are out of balance with the planet and society. We are challenging ourselves in many ways to break this cycle and to keep our shoes and clothing from entering landfills. That includes making products that last longer, introducing ways to extend your use, and repurposing them when you are done.
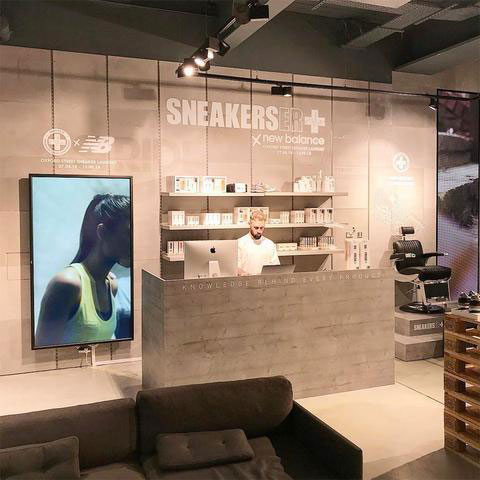
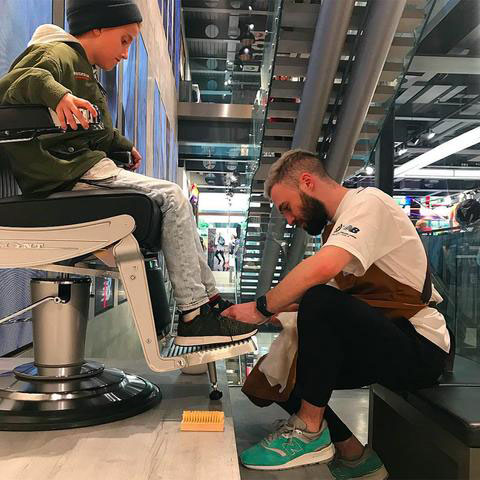
Care: The first step is taking good care of your shoes so they can last longer and keep logging miles. You can find some suggested cleaning tips here. New Balance also connected with SneakersER to create a Sneaker Laundry inside our Oxford Street store in London.
Repair: In Japan, New Balance offers a shoe repair service that focusses on common repair needs, like soles and collar linings. The service is offered in Japan across our Made models, and we repair approximately 3,500-4,000 shoes per year.
Take-back: Many New Balance stores take back gently worn shoes from our customers, donating usable items to local organizations or Soles4Souls. In the U.S., these programs are in place at approximately two-thirds of our licensed stores.
We continuously learn through these programs and have some exciting new plans in development, so you will see even more of this to come!
The New Balance Restricted Substance Program is designed to protect the environment where we make our products, the health of workers in those manufacturing facilities, the health of our consumers, and our brand integrity. It applies to all footwear, apparel, accessories and equipment that New Balance makes (both in our own factories and our contract factories) as well as to all products made by our licensees.
OUR PROGRAM COVERS FOUR CORE ELEMENTS
- Restricted Substances Manual and Audits
- Product Chemistry Training
- Restricted Substances List (RSL) Certification
- Product Safety
All New Balance footwear is polyvinylchloride (PVC)-free and we prohibit the presence and/or use of toluene in raw materials or manufacturing. We also encourage suppliers to bring safer, alternative materials and chemicals to us proactively and implement continuous improvement programs around chemical safety.
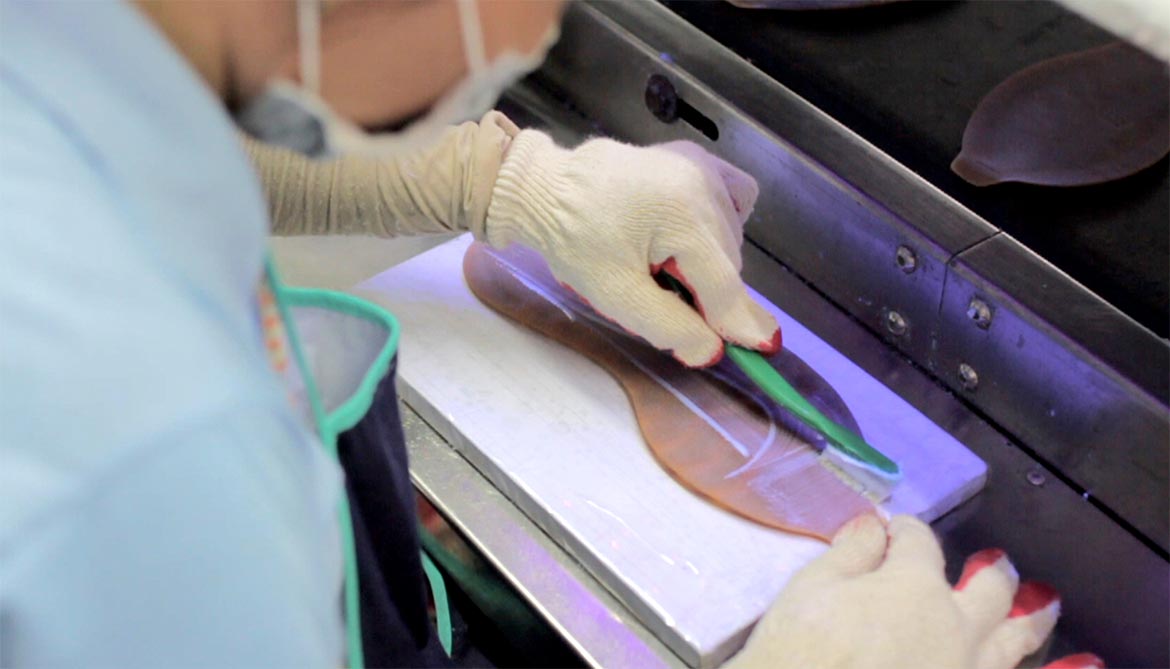
The core of our program is the New Balance Restricted Substances Manual (RSM) that enables our suppliers to make safer and more sustainable chemistry choices. The RSM prohibits some chemicals, sets limits for others, and specifies testing requirements and methods that our suppliers must use to demonstrate they are complying with New Balance requirements. We update the RSM annually to ensure that materials and methods used in our manufacturing comply with the strictest global requirements (RSM Summary of Changes). The Manual covers more than 380 chemicals and incorporates legislation and regulations covering the US, Europe, Japan, China and other countries, along with California's Proposition 65.
The RSM is incorporated into New Balance supply agreements. Factories and suppliers are also required to sign a written acknowledgement of the RSM and maintain a Chemical Information List (CIL) itemizing the chemicals used in the facility. Suppliers must also submit products for regular testing conducted by third-party laboratories. Each year, our Product Chemistry team also conducts audits in selected footwear factories and subcontractors to ensure chemical compliance with the RSM.
If products are found to contain a restricted substance, the Product Chemistry team works with suppliers to identify the root cause of the chemical failure. Changes or replacements must be made before the product can be sold.
In April 2013, New Balance joined the Zero Discharge of Hazardous Chemicals (ZDHC) Roadmap to Zero Programme – a coalition of major apparel and footwear brands and retailers that are committed to lead the industry towards zero discharge of the industry’s most hazardous chemicals. ZDHC has put forth a roadmap that demonstrates the collaborative efforts of the organization and how ZDHC contributors intend to lead the apparel and footwear industry towards better chemical management.
New Balance played a leadership role in helping ZDHC develop the ZDHC Manufacturing Restricted Substances List (ZDHC MRSL) and Conformity Guidance. Where the New Balance Restricted Substances List is specific to chemistry found within the final product, the ZDHC MRSL addresses a broader set of chemicals that might be present in the manufacturing environment. The ZDHC MRSL is a list of chemical substances banned from intentional use in facilities that process textile materials and trim parts in apparel and footwear. The ZDHC MRSL establishes acceptable concentration limits for substances in chemical formulations used within manufacturing facilities. These limits are designed to eliminate the possibility of intentional use of listed substances. The intent of the ZDHC MRSL is to manage the input of chemicals to the suppliers and remove hazardous substances from the manufacturing process.
The Product Chemistry team includes materials engineers based in China, Vietnam and Indonesia. This team works to improve chemical and product safety management at key footwear and apparel suppliers throughout Asia. In coordination with the Global Compliance team, they deliver trainings to Tier One suppliers on topics related to New Balance restricted substances and best practices in chemical management. Trainings and workshops to date have included an overview of global footwear regulations, trends in footwear recalls, review of children’s footwear safety standards and testing practices, and the importance of establishing internal control measures to reduce or eliminate restricted substances in products and reduce exposure for workers.
Suppliers are also encouraged to enroll in online training to fully understand their responsibilities related to New Balance’s restricted substances requirements.
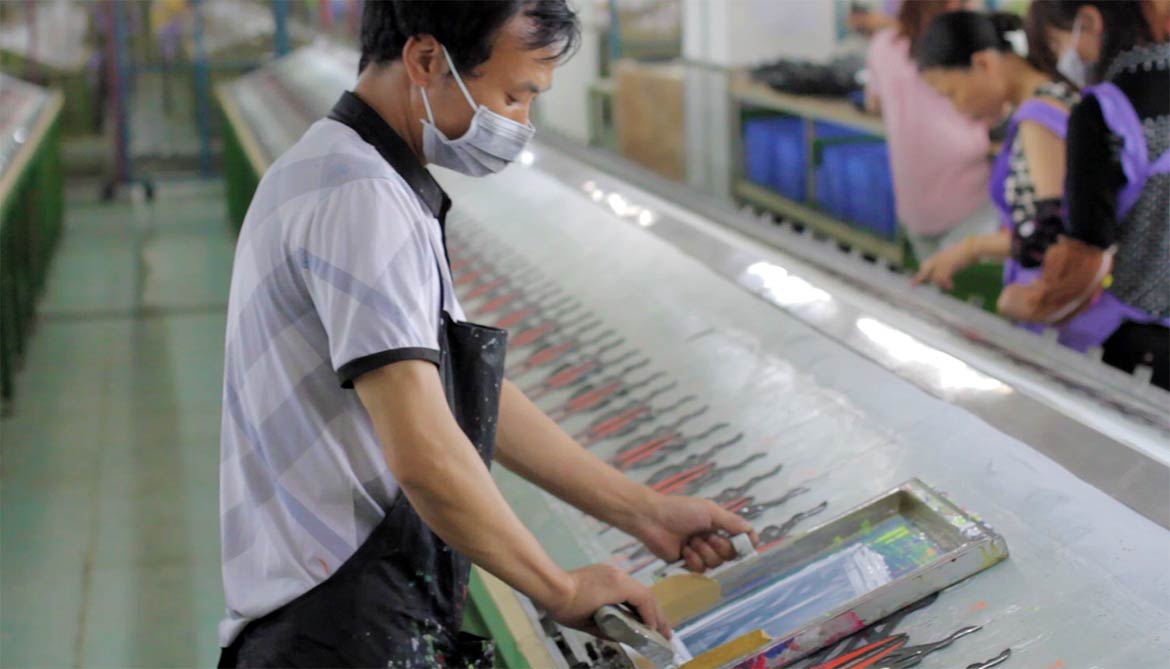
In an effort to strengthen relationships with suppliers regarding chemical management and restricted substances compliance, New Balance implemented a Restricted Substance List (RSL) Certification Program. RSL-certified suppliers maintain strong internal chemical management systems aimed at preventing RSL-related problems with materials. Certified suppliers are categorized as Gold, Silver and Bronze. We audit suppliers based on a set criteria including upper management commitment, documentation of policies and procedures regarding RSL compliance, chemical and risk management, raw materials management and manufacturing process control, multiple supply chain controls, and corrective action and performance improvement plans.
New Balance is committed to ensuring our products are safe and in compliance with global laws and regulations. New Balance maintains a robust program to verify product compliance with safety standards. Suppliers must submit products for third-party lab testing and undergo regular training to ensure continued awareness of and compliance to applicable product safety requirements.
The New Balance Product Safety program includes compliance with the US Consumer Product Safety Improvement Act (CPSIA), which requires manufacturers to certify that their products comply with applicable safety rules, bans or standards using accredited third-party testing labs. To search for a certificate of compliance, please visit www.NBCPSIA.com.
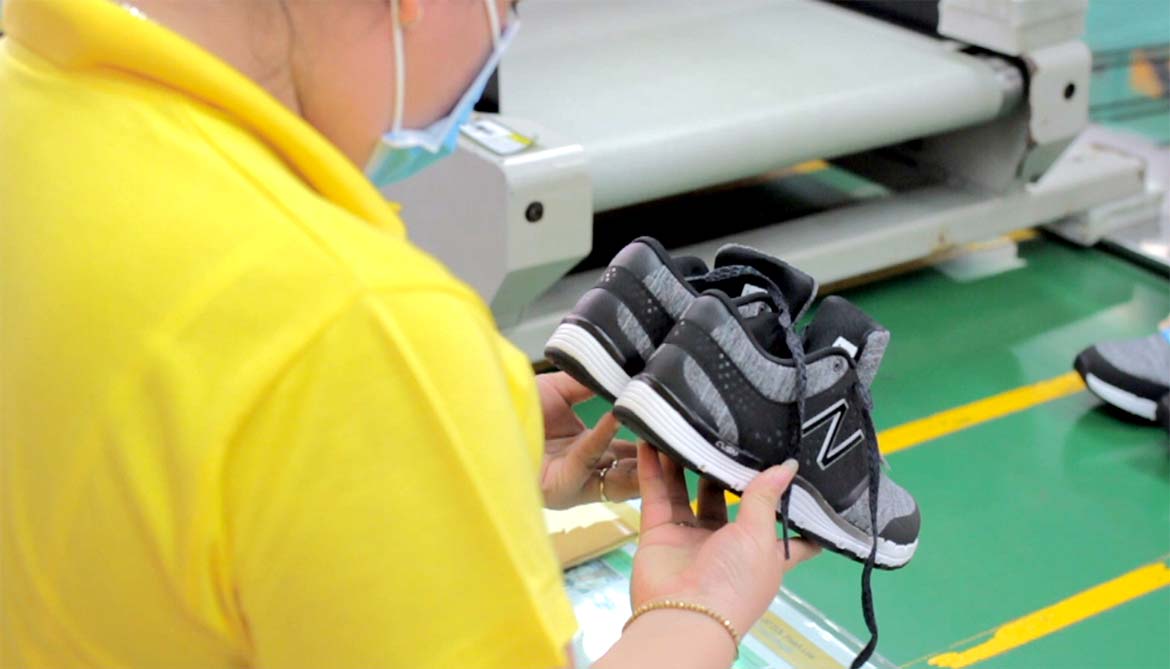
New Balance’s primary footwear packaging consists of a one-piece seamless designed shoebox that integrates a flip top lid with the shoebox base. The packaging inside the box consists of wrapping tissue that is used to separate and protect the shoes, and also toe stuffing tissue used to protect the shoe tip and maintain product quality.
Our core shoeboxes are made from 100% recycled paperboard, consisting of pre- and post-consumer pulp and are 100% recyclable. Our master shipping cartons are also made from pre- and post-consumer pulp with approximately 44% virgin fiber. All inks are soy-based. Starting in 2018, we changed the weight of our wrapping tissue from 28gsm to 22gsm, which reduced our annual paper usage by 130 tons. New Balance continues to seek opportunities to eliminate packaging waste from our supply chain and optimize packaging solutions.
New Balance catalogs, which are used for marketing and direct consumer sales in the US, are also printed on 100 percent FSC- and SFI-certified paper.*
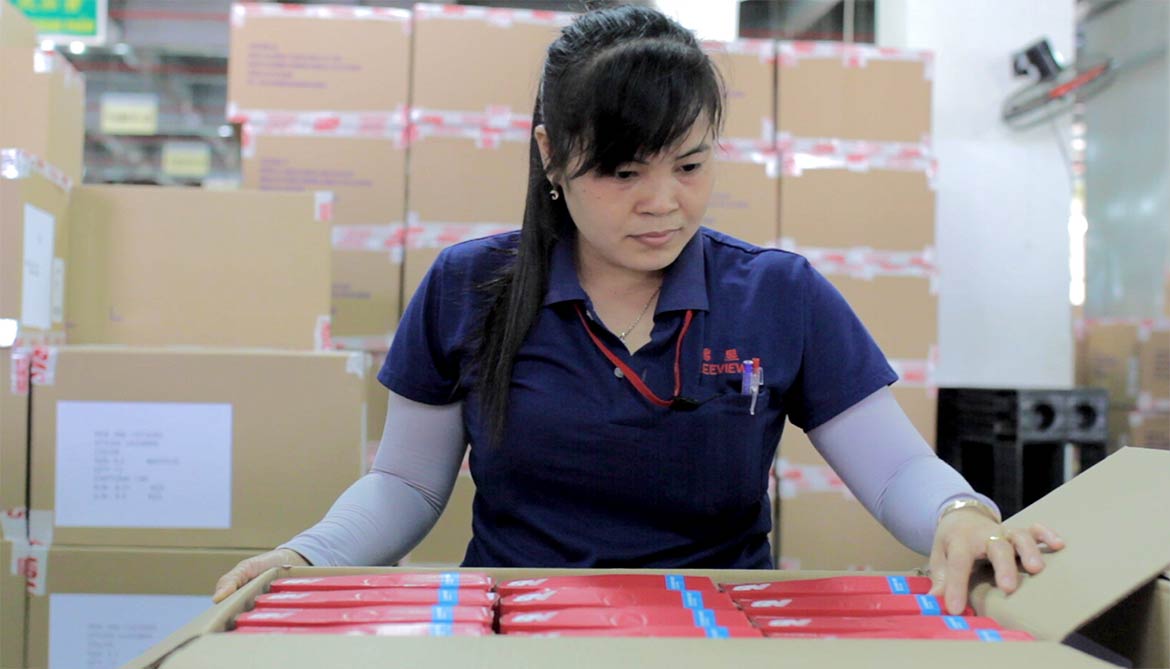