Responsible
Leadership
New Balance builds global brands that athletes are proud to wear, associates are proud to create and communities are proud to host.
OWNED MANUFACTURING
New Balance has remained firm in our commitment to owning and operating footwear manufacturing facilities in the United States and United Kingdom. Our success has been built and sustained by our unwavering belief that making things matters and the multi-generational craftsmanship of the men and women who work in our factories.
New Balance has a long-standing commitment to owning and operating manufacturing facilities – we strongly believe that making things matters. Our success has been built and sustained by the multi-generational shoemaking craftsmanship of thousands of men and women who work in our athletic footwear factories in the United States and the United Kingdom. Manufactured in the U.S. for more than 75 years and representing a limited portion of our U.S. sales, New Balance Made U.S. is a premium collection that contains a domestic value of 70% or greater.
Since Jim Davis purchased New Balance in 1972, our global sales have grown from $1 million to $4 billion and our associate population has swelled from six to more than 8,000 associates.
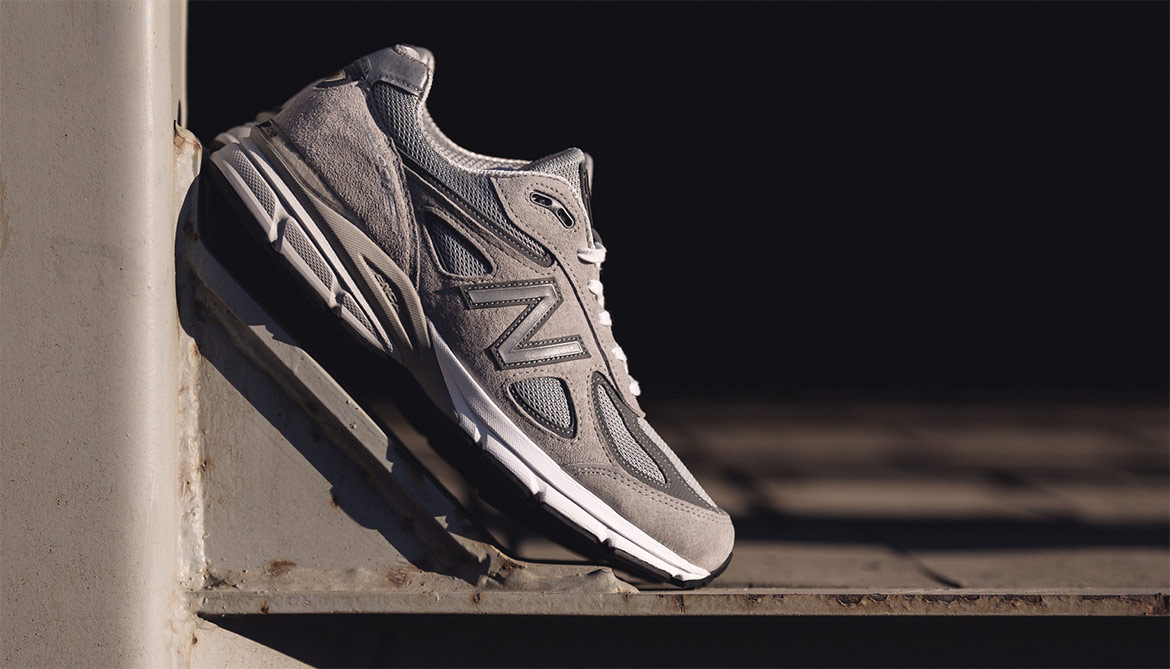
HOME FIELD ADVANTAGE
Our decision to maintain footwear production in the United States bucked industry trends to move manufacturing overseas. When New Balance was growing rapidly in the 1970s and 1980s, as well as when tough economic times hit in the 1990s, company owner Jim Davis recognized that local production provided important proximity to U.S.-based research and development, enhanced responsiveness to customers and reflected the community-focused values of the company.
U.S.-based athletic footwear production has given New Balance another competitive advantage: craftsmanship. Our manufacturing expansion into Maine in 1981, for example, capitalized on a talented base of shoemaking expertise. Today, many of our associates in Maine have worked at New Balance for decades some have inherited their shoemaking passion directly from family members.
At our U.K. facility in Flimby, the New Balance commitment to domestic manufacturing is the same. We honor Britain’s legacy as the workshop of the world while serving a growing European market.
SPURRING INNOVATION
New Balance believes that maintaining our own athletic footwear production allows us to accelerate innovation. We can test new ideas, encourage collaboration between our design and manufacturing teams, and learn first-hand from continuous improvement efforts. In 1978 we introduced modular assembly teams and, later, lean manufacturing – both instrumental process innovations that have helped us stay competitive.
More recently, our manufacturing capabilities in Massachusetts and Maine allowed us to offer an unparalleled three-day turnaround for U.S. consumers of NB1 custom athletic shoes, giving New Balance a distinct competitive advantage in the growing custom shoe market.
BENEFITS BEYOND THE FACTORY GATE
Owned manufacturing promotes economic development in our communities through the employment of more than 1,600 manufacturing associates in our U.S. and U.K. operations, as well as through our support for local suppliers.
We are committed to being active partners in the communities where we live, work and play. Through philanthropic support and volunteerism, we are helping to build healthier, stable and sustainable communities. To read more about these initiatives, click here.
made. american. is our commitment to manufacturing in the United States and delivering the highest quality shoes to our customers across the globe. We are proud of our unique history. In our second century of business, our shoes are built on 75 years and three generations of American craftsmanship, providing a strong foundation for future growth as we usher in a new era of domestic manufacturing.
That foundation began in 1972, the year Jim Davis purchased New Balance, and the six employees who managed manufacturing and distribution out of our 10,000-square-foot Belmont Street facility in Boston’s West End. Five years later, amid the 1970’s running boom, the New Balance 320 model was rated #1 by Running World, catapulting the brand to the forefront of modern athletic shoe design.
To respond to skyrocketing demand, the company more than doubled its Boston manufacturing space in 1977.
Further expansion quickly followed, first to Lawrence, MA in 1978, then to Skowhegan, ME in 1981, where the Norwalk Shoe Company had closed shop, leaving a highly skilled workforce and ample manufacturing space. Norridgewock, ME followed in 1982 and then Norway, ME in the mid-1990s.
Today, these facilities employ approximately 1,000 associates. In 2015 we cemented our commitment to these New England communities with the opening of a new global headquarters at Boston Landing. Located at the western entrance to Boston, it makes a highly visible statement that New Balance has and will remain invested in our associates here and the communities where we first began.
Five Words of Inspiration
How do you sum up years of working together in a team that feels like family? Five of our Lawrence manufacturing employees managed to punctuate its essence: Opportunity. Teamwork. Support. Family. Pride.
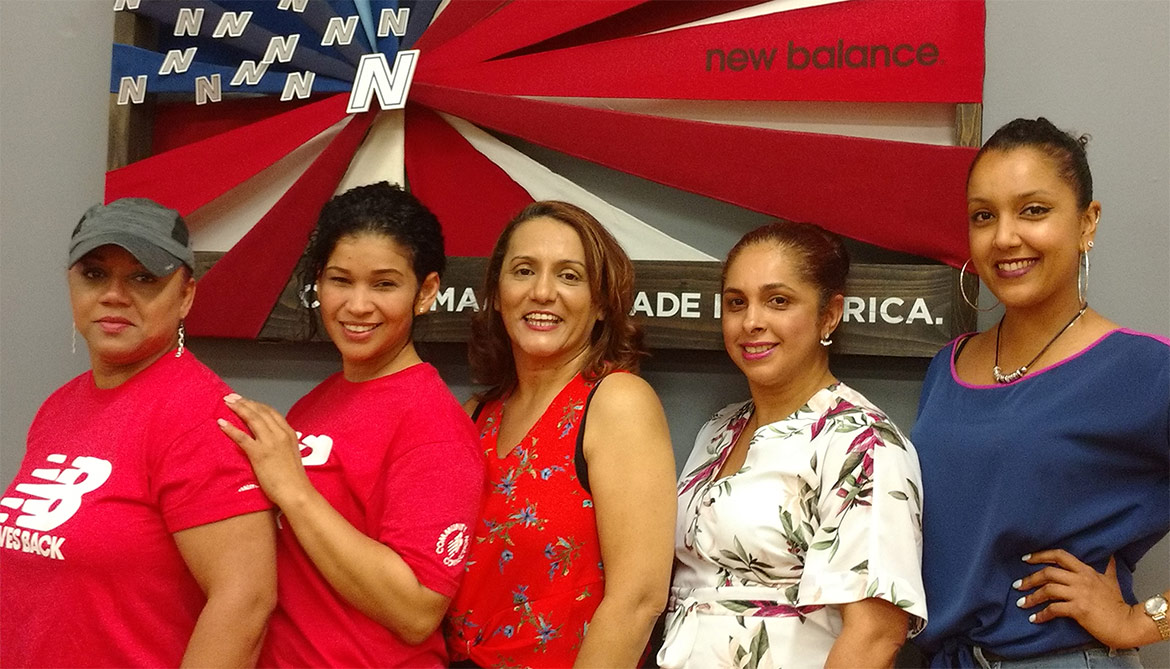
Opportunity
“New Balance gave me the opportunity to take English classes and take part in the [13-month-long] Leadership in Training program. At first I didn’t want to go, I made excuses. Now, I’m open to learn everything. I’m not afraid.”
- Arelis Villa Roman, Green Line Manufacturing Supervisor in Training, Lawrence employee for 15 years
Teamwork
“We work as a team. We meet everyday to discuss what help we need to meet our goals, and everyone is willing to help.”
- Lucy Jimenez, NB1 Custom Pre-fit Team Leader, Lawrence employee for 13 years
Support
We always support each other when we need it, at work and outside of work. Even when we have a personal situation, the leadership and the whole team gives support.”
- Martina Rosa, Kaizen Associate, Lawrence employee for 10 years
Family
“Celebrating New Balance’s 100 years taught me how long the company has been around, how much the company has grown and how big it is. And still, they treat us as a family and they care for us, not only as associates, but as a family too.”
- Dulce Pita, Kanban Associate, Lawrence employee for 21 years
Pride
“My most memorable day is Family Day, when my daughter, my granddaughter and my husband came here [to the factory]. They were so proud. I feel very proud to be working for a New Balance because they gave me an opportunity to grow personally and professionally.”
- Yokasta Almonte, NB1 Custom Team Manufacturing Supervisor, Lawrence employee for 17 years
made. british. is New Balance’s commitment to more than three decades of refined craftsmanship that defines the premium quality, high-end athletic footwear we produce in Flimby, United Kingdom.
Founded in 1982, our Flimby facility builds on more than 35 years of production and three generations of local craftsmen and women. In the mid-1980s, more than 80,000 people manufactured footwear in the U.K. and now there are fewer than 4,000 withabout 250 of them employed at New Balance. A new 21,500-square-foot company warehouse located near the facility was recently constructed to help meet growing demand.
As it does in the United States, domestic manufacturing in Flimby provides New Balance the flexibility to meet customer demand on short lead times. Building on Britain’s legacy as the workshop of the world, a dedicated and highly skilled workforce, a reputation for product quality and a global fan following, New Balance is proud of its commitment to made. britain.

“I have been at New Balance for 35 years, and there have been a lot of changes. Technology has changed – we now use robots to cement and rough – and we produce a lot more shoes in a year than we used to. Throughout the changes New Balance has secured a lot of jobs for people in Flimby and nearby Workington and Whitehaven. They also give a lot back to the community and to our schools.”
- Tom Ross, Multi-skilled Associate, Flimby employee since 1982, the year the factory opened
“Jim Davis opened the doors in 1982 when a lot of people were taking manufacturing offshore. One of his reasons was the shoemaking heritage here. In addition, there is a great work ethic. It never ceases to amaze me how our associates are open to change. They know we’ve got to keep improving, and even though it’s difficult to adjust when you’re under pressure to deliver orders, they are engaged in helping us change for the future.”
- Andy Okolowicz, Factory Manager, Flimby employee since 1997