Responsible
Leadership
New Balance builds global brands that athletes are proud to wear, associates are proud to create and communities are proud to host.
Environment
New Balance is taking significant steps to ensure a healthier planet. We are constantly looking for ways to minimize and prevent negative environmental impacts in our operations and throughout our global supply chain – with an eye towards zero impacts and bringing greater positive change to our local environment.
We live in a community greater than just our company. Our products – and the materials that go into making them – are processed with energy, water, and chemicals in factories around the world. We are working hard to understand and minimize negative environmental impacts of our supply chain operations – with an eye towards a future where we leave zero impacts and even bring positive change to the local environment.
Our environmental efforts are focused on different strategic priorities in different levels of our supply chain.
Tier 1 | Tier 2 |
---|---|
We monitor basic environmental compliance through our audits and are helping suppliers invest in meaningful energy efficiency and carbon reduction initiatives. | We are focused on water risks and require suppliers with wet processing capabilities to test their wastewater discharge according to the ZDHC Wastewater Guidelines developed by the industry leading ZDHC Roadmap to Zero Programme. |
Both Tier 1 and Tier 2 suppliers are screened quarterly against the Institute of Public & Environmental Affairs (IPE) database for environmental violations in China and undergo broad environmental assessments using the Sustainable Apparel Coalition (SAC)’s Higg Facility Environmental Module (Higg FEM). |
New Balance was one of only six companies to step forward and be featured on a new online map that links brands to their suppliers’ environmental performance in China. The IPE Green Supply Chain Map was launched in January 2018 by the Natural Resources Defense Council (NRDC) in the US and the Institute of Public & Environmental Affairs (IPE) in China.
“These companies that have stepped up to put their names first on the inaugural map are showing new levels of transparency on their manufacturing abroad and are demonstrating real leadership in supply chain responsibility,” said Linda Greer, senior health scientist for NRDC and founder of its Clean by Design green supply chain program.*
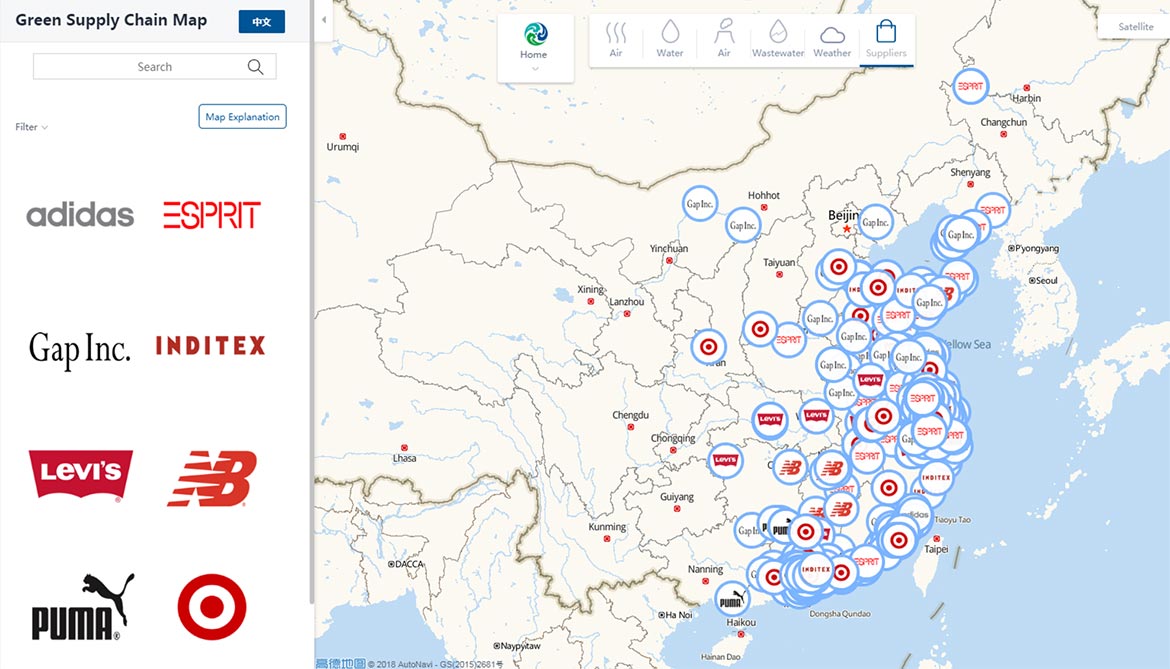
For the first time, factory pollution data for suppliers can be viewed in nearly real time by the public. Map users can click on our brand logo and see how the supplier factories are performing at that moment, as well as 30-day trends of air emissions and wastewater discharge, environmental violation records and factory responses.
In 2017, New Balance ranked 16th of 267 companies in the Corporate Information Transparency Index (CITI) that evaluates brands according to how well they address supply chain environmental responsibility in China. In 2018, we climbed to 11th overall.
New Balance is proud to be a founding member of the Sustainable Apparel Coalition (SAC), joining the coalition in 2011 as groundbreaking work began on the first industry-wide environmental indexes. Today, the SAC is an alliance of over 200 brands, retailers, manufacturers, academics, NGOs and other affiliates – representing over $500 billion in revenue. The SAC’s collective vision is of an apparel, footwear and textiles industry that produces no unnecessary environmental harm and has a positive impact on the people and communities associated with its activities.
Peers and competitors work together to redefine how the industry is run. Members commit to transparency, the sharing of best practices and making meaningful improvements that can be measured according to a standardized set of tools, called the Higg Index.
The Higg Index is the heart of the SAC, developed by the SAC and its members. The Higg Index is a suite of tools that enable brands, retailers and facilities of all sizes to measure and score various aspects of sustainability performance. Ultimately, the Higg Index empowers organizations across the global supply chain to precisely identify areas requiring improvement and highlight robust actions to take.
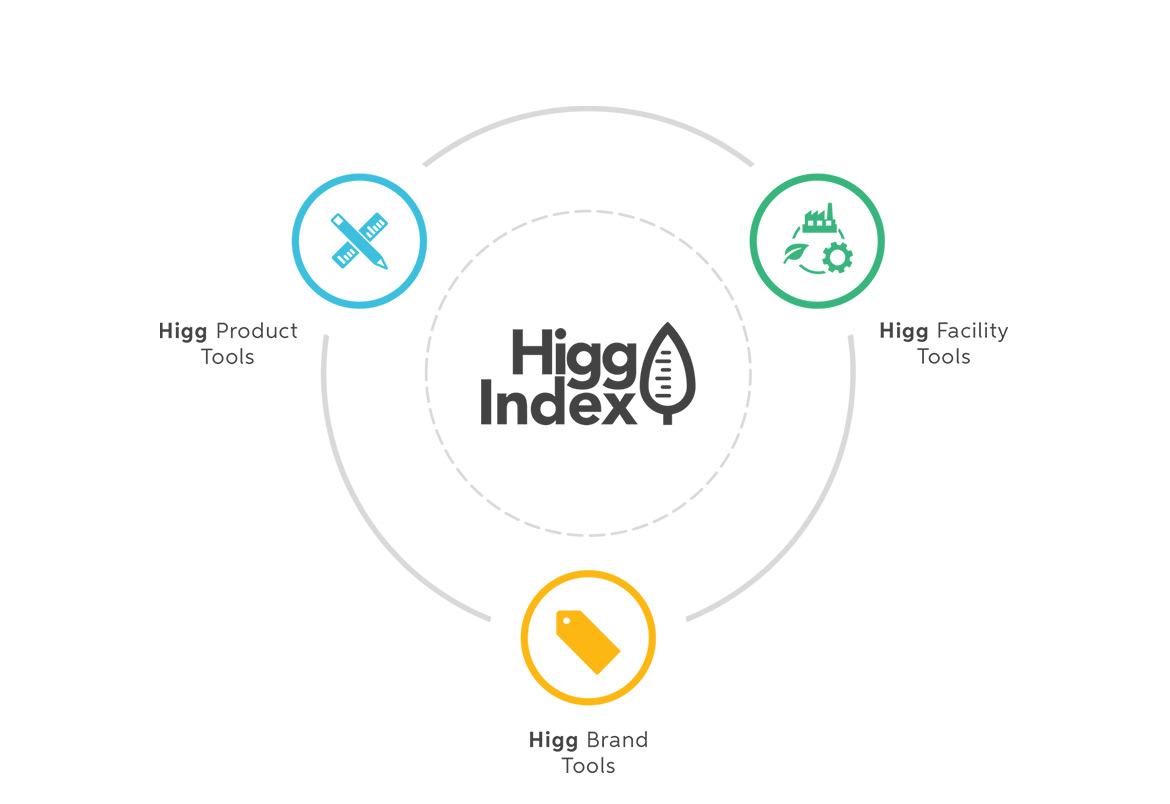
1. Brand tools, for assessing overall sustainable practices by brands and retailers
2. Product tools, for understanding and assessing lifecycle impacts of products
3. Facility tools, for measuring environmental and social impacts in manufacturing facilities
New Balance played an active role in developing and testing the Higg Index, and we have implemented the available tools within our company and supply chain. We have been exploring how to use lifecycle data within the Higg Materials Sustainability Index (MSI), and New Balance continues to use the Higg Brand and Retail Module (Higg BRM) for internal planning and benchmarking purposes.
We used the Higg Facility Environmental Module (Higg FEM) 2.0 to assess our Tier One footwear suppliers in 2015 and used those results to inform improvement efforts at the factories. In 2017, four New Balance suppliers participated in the Higg FEM 3.0 pilot, or “pressure test,” and we are now in the process of rolling out the updated Higg FEM 3.0 to about 80 suppliers in total, including all Tier One footwear suppliers, key Tier One apparel, and some of our largest Tier Two material suppliers.
As part of the global community, we have a responsibility to understand, mitigate and adapt to the effects of climate change. We are continuously learning about how climate change may impact our business, how our business impacts climate change, and how we can responsibly contribute to global climate goals .
New Balance is moving toward a low carbon future by reducing energy consumption in our own facilities and throughout our global supply chain, and by actively investing in renewable energy. We are in the process of completing our first company carbon footprint, which will serve as the basis for prioritizing future initiatives and setting company-wide targets.
New Balance has been working for several years to improve overall energy performance in footwear suppliers, with the goal of reducing costs and greenhouse gas emissions. In 2014, we set a goal with our Tier One footwear suppliers to reduce energy use per pair by 10% within three years. The goal was modest but achievable, and we believed that it would spark momentum for further action. By the end of 2017, our footwear suppliers collectively reduced their energy use by 21.5% per pair – almost double the original 10% target. Several strategic factories have seen reductions over 30%.
The first year of the program focused on planning and capacity building and resulted in each factory creating its own Energy Efficiency Plan that prioritized energy conservation measures and action plans. New Balance then worked with suppliers to identify energy champions, create energy teams, undertake trainings, and conduct energy walk-throughs to familiarize the teams with key operations – which included learning about energy tracking, discovering where energy is used most, and finding energy saving opportunities.
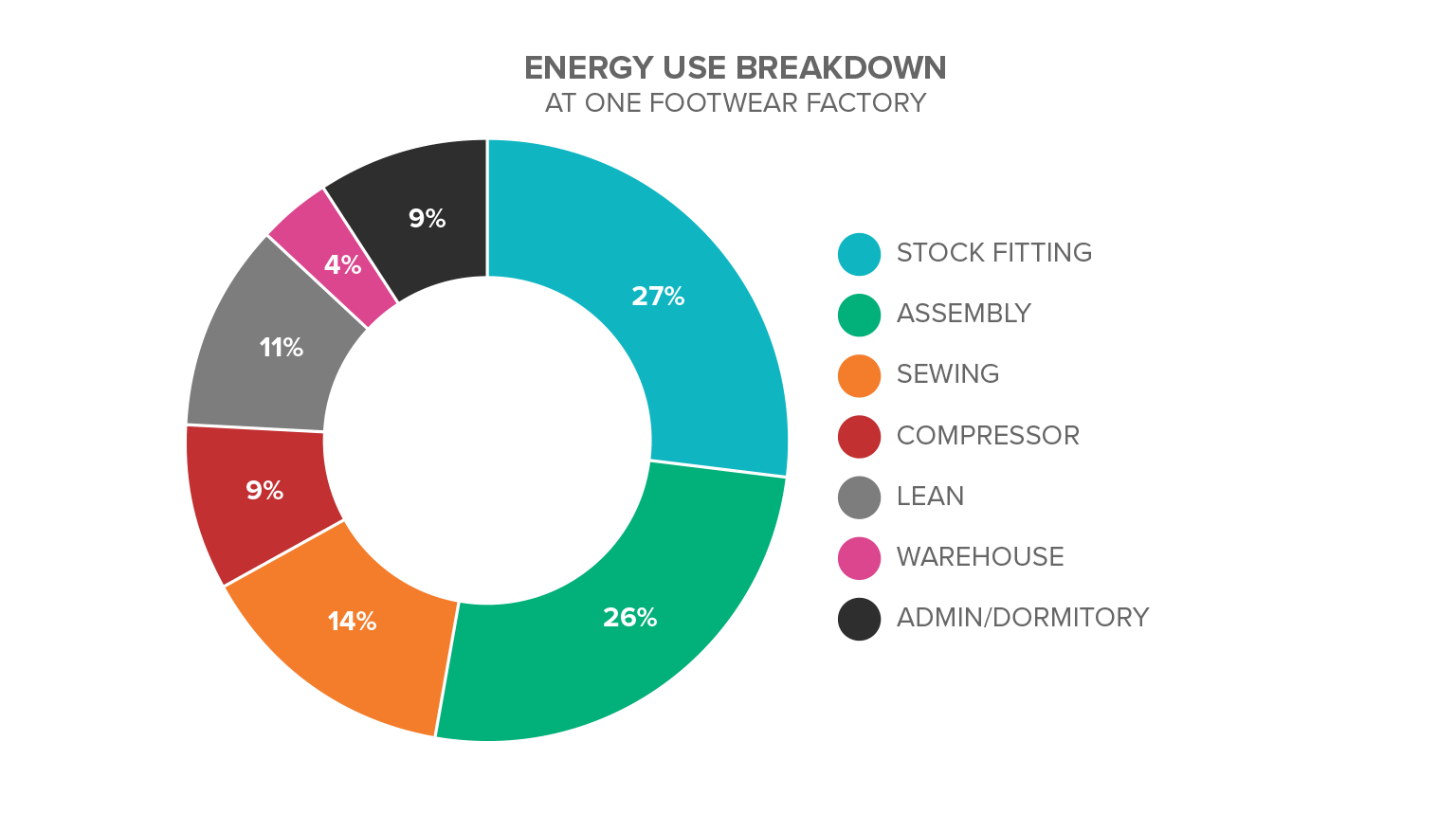
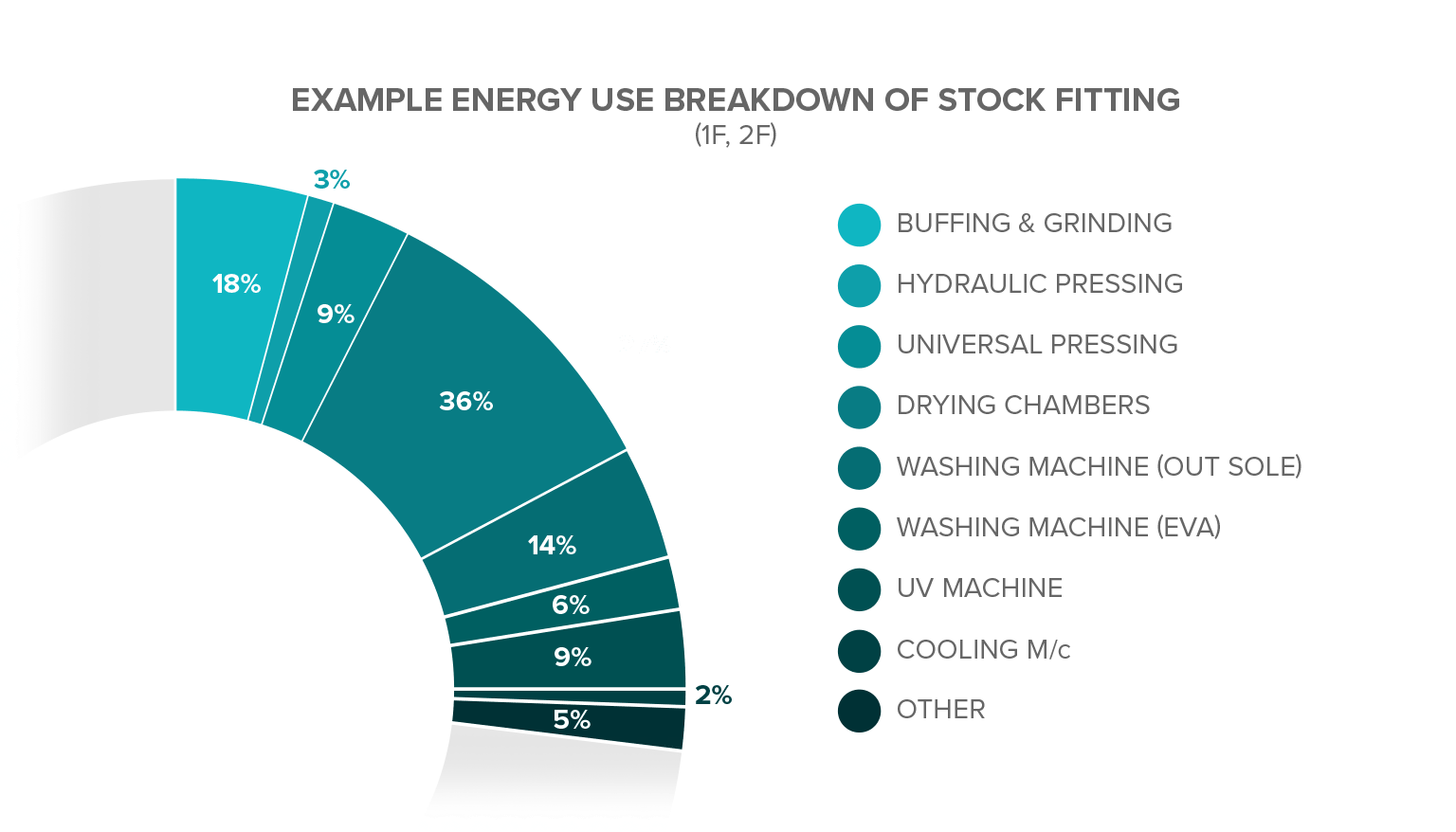
We also integrated energy as a regular topic into our supplier workshops in China, Vietnam and Indonesia and redesigned our Environmental Impact Data (EID) system to allow suppliers to report and track monthly energy use more consistently. In 2017, we conducted 36 hours of energy training for 48 suppliers in China, Vietnam, and Indonesia.
In 2015, one of our New Balance Facility Managers from a New Balance-owned manufacturing facility in Maine visited Vietnam and conducted workshops to teach suppliers how to improve their compressed air systems, which are notorious for leaks and other inefficiencies. Our goal was to heighten the understanding of energy use in factories, share our own experience as a manufacturer, and highlight manufacturing processes and workshops that use the most energy. It was a great learning experience for all sides, and suppliers appreciated the fact that New Balance is tackling the same challenges in our own factories.
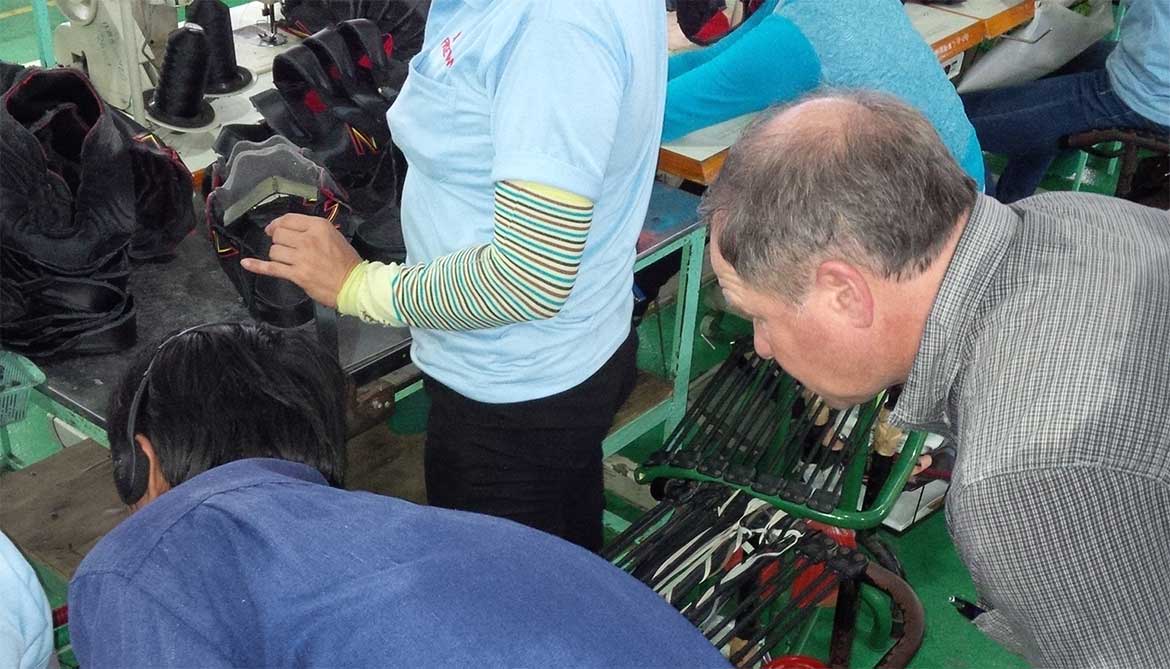
In 2015, New Balance became one of the first footwear brands to join the Carbon Performance Improvement Initiative (CPI2), providing suppliers with an easy-to-use online energy assessment tool that generates key energy-saving recommendations. This tool has become a foundation of our energy program and provides suppliers a systematic way to approach energy savings without having to hire external consultants (although some do). All New Balance footwear suppliers are now using CPI2. We are expanding tool usage with key apparel suppliers, some equipment suppliers in China and one of our owned equipment factories in Finland. Today, we have 28 participating suppliers in 10 countries. One of our apparel suppliers, Bodyline (Pvt.) Ltd., an affiliate of MAS Group of Companies, in Sri Lanka, was awarded second place for CPI2’s Top Factory in 2017 by CPI2 and its user community.
In China, New Balance has hosted an Environmental Defense Fund (EDF) Climate Corps fellow for three years in a row (2015-2017). EDF expanded their renowned fellowship program into Asia, offering a great opportunity to apply their Climate Corps process to extended supply chains. See the links below for more information on the annual fellows.
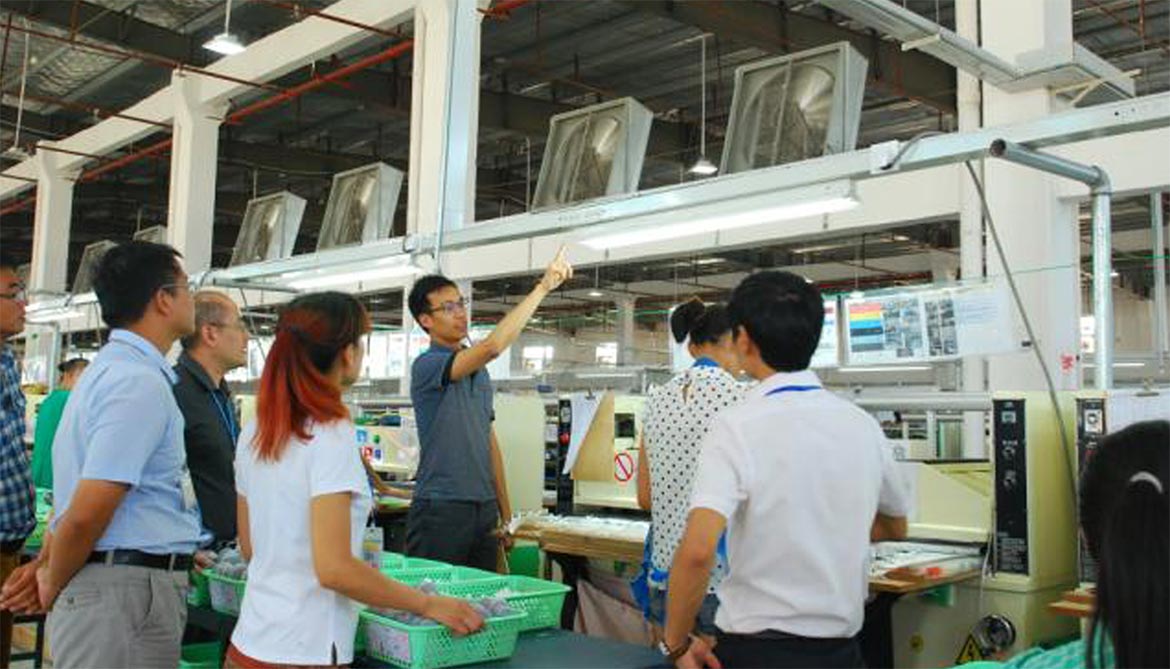
Year | Fellow | Net Present Value | Annual kWh Savings | Annual C02 Reductions |
---|---|---|---|---|
2015 | Yien Huang | $180,000 | 805,000 | 423 MT |
2016 | Xiu Yujiao | $190,000 | 435,000 | 400 MT |
2017 | Sheng Cao | $140,000 | 310,000 | 170 MT |
In Vietnam, New Balance became one of the first footwear brands to partner with the International Finance Corporation (IFC) in 2016 to launch the IFC’s Vietnam Improvement Program (VIP) for driving sustainability in the apparel, textile and footwear sector. Together with other footwear and apparel brands, we are using our collective power to drive behavioral change across the industry and contribute toward Vietnam’s national green growth plans. Two of our key footwear suppliers are participating in the program. They were selected because they had been falling behind our energy reduction goals. The VIP program assesses overall resource efficiency and clean energy options at supplier factories through detailed engineering assessments, training, and developing programs that reduce operating costs and improve productivity. IFC’s program is unique in that it also helps factories with access to financing for larger, more complex projects that otherwise might not be available. The goal is to facilitate real action, not just an assessment report that sits on the shelf.
One facility identified opportunities that would save 14% of electricity, with potential of up to 31% savings depending on how broadly the measures are adopted throughout all workshops. The second facility identified opportunities to save 12% across eight workshops.
-
KEY ENERGY SAVING OPPORTUNITIES INCLUDED:
- Repairing compressed air leakage, shutoff/isolation valves, and automatic moisture traps
- Automatic buffing machines and cutting machines
- Variable frequency drives on large motors
- Insulation of hot plates on no-sew pressing machines
- Servo motors on cutting machines and stitching machines
- Infrared heaters and dryers to replace electric
- LED lighting conversion
- Improvement in Right-First-Time lean production processes
14-31%
Energy Savings
We will apply these learnings from VIP to other footwear suppliers.
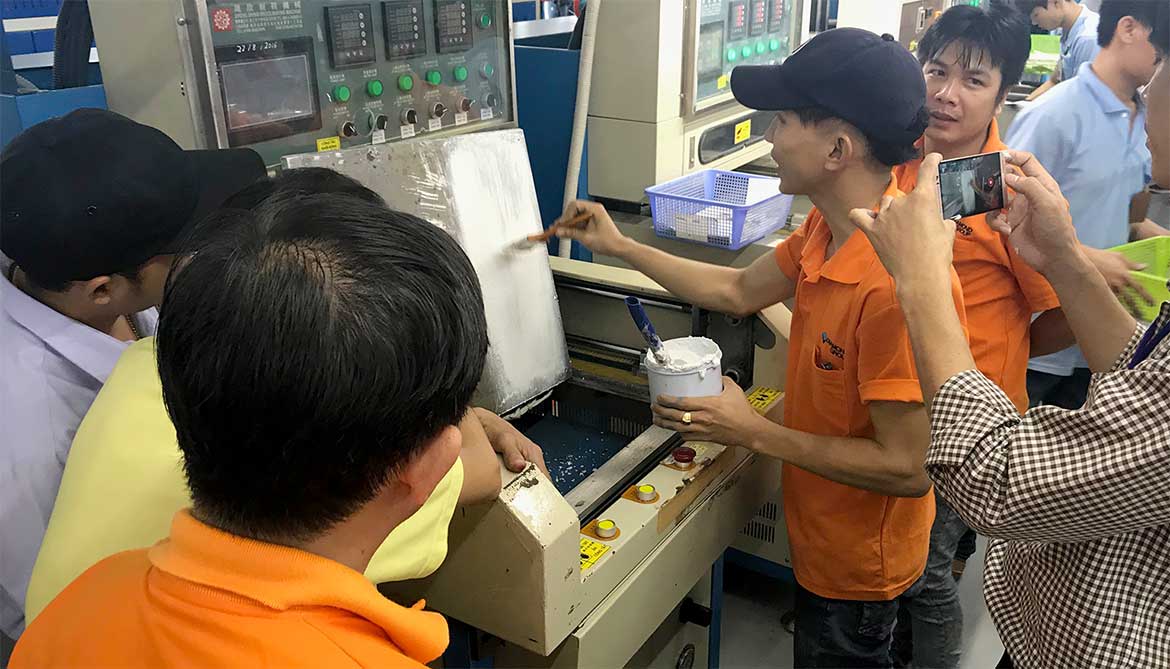
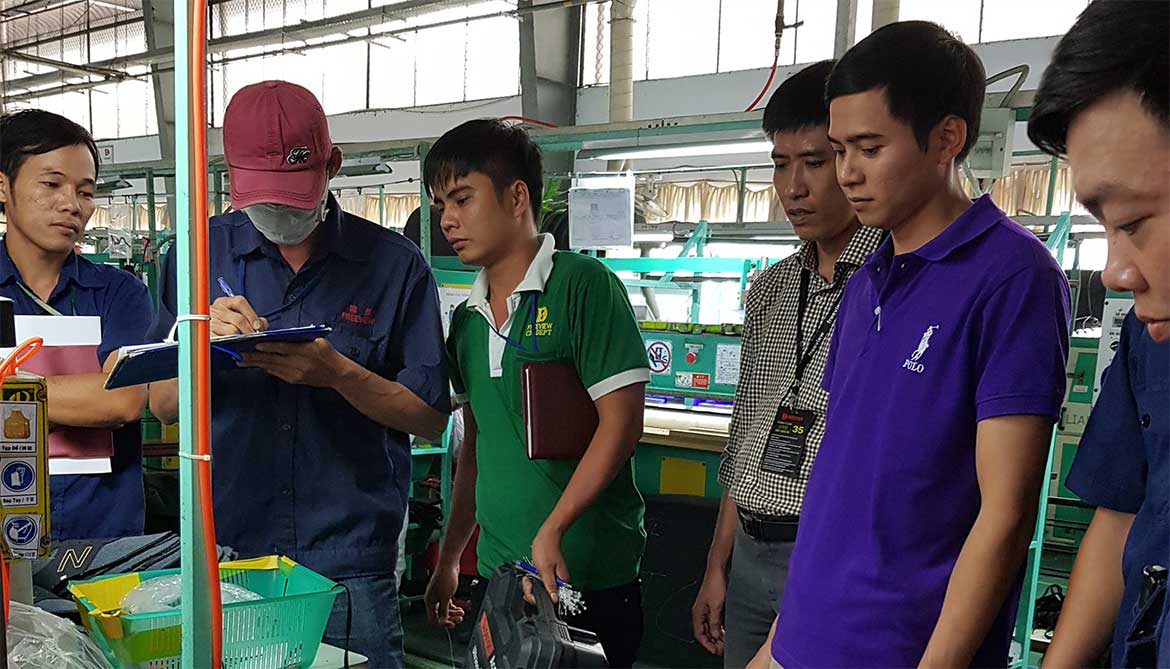
New Balance works closely with its supplier factories to reduce energy, greenhouse gas (GHG) emissions and costs. We focus our attention on Tier One footwear factories and Tier Two mills and tanneries, which represent a significant portion of our Scope 3 emissions. Starting in 2015, we have worked closely with the Clean by Design (CBD) program and the International Finance Corporation’s Vietnam Improvement Program (VIP) to bring essential outside expertise into the factories and mills.
Six of our key textile mills have participated in or are still in process of running the CBD program in China and Taiwan (ROC). Four of those mills that completed the program identified GHG reductions of 3,950 MTCO2 and freshwater savings over 1.3 million cubic meters.
Shinkong Textile is a recent mill participant in the 2019-2020 CBD cohort. After a thorough assessment, the Shinkong team selected eight energy and water conservation measures for implementation. Their top opportunities included condensate water recycling, insulation for steam pipeline and valves, replacement of an obsolete air compressor, improved dyeing volume by unit and a metering system to enable more effective ongoing energy management. All measures were completed by June 2020, half year ahead of schedule.
By participating in the CBD program, Shinkong received valuable assistance and identified annual GHG reductions of 824 MTCO2 (equal to 12% of its total), water savings of 32,455 m3 (equal to 7% of its total consumption), and cost savings of $168,000.
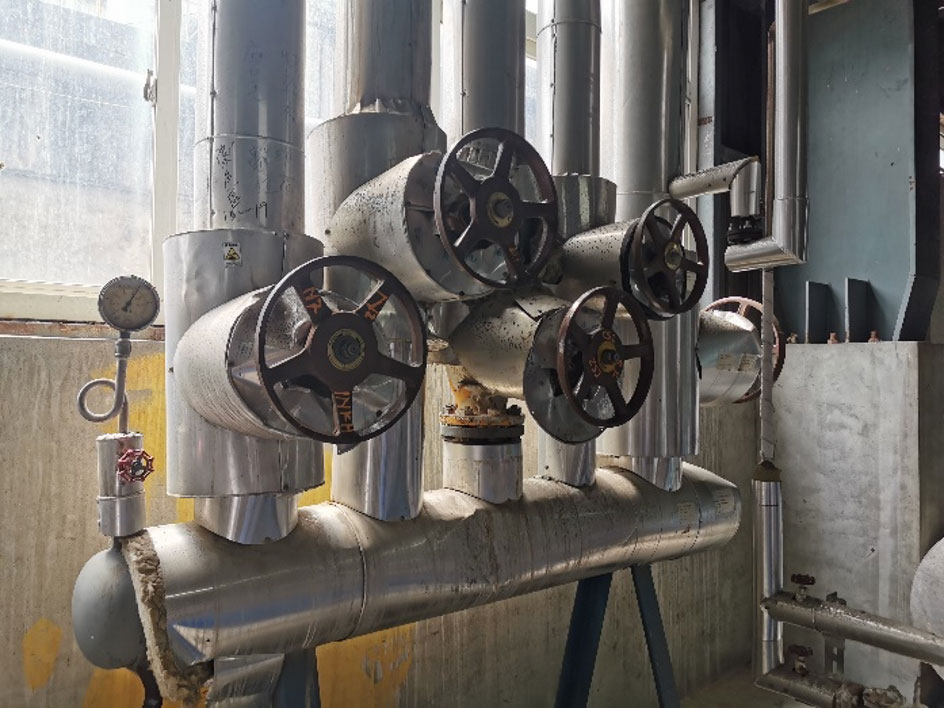
Moving towards a low carbon future is a core part of our global Responsible Leadership program and illustrates how New Balance seeks to do business with purpose and integrity. Clean energy is good for the environment, good for public health, and good for business. We believe now is the time for action and collaboration to affect positive global change.
At New Balance, we’re focusing our efforts around two major climate commitments: joining RE100 and signing the United Nations (UN) Fashion Industry Charter for Climate Action.

Through RE100, New Balance commits to sourcing 100% of its electricity from renewable sources by 2025 across all global New Balance operations. RE100 is a global initiative that brings together the world’s most influential companies committed to 100 percent renewable power. The goal is to increase corporate demand for renewable energy and spur greater renewables development which is critical in transitioning to a net-zero emissions economy.
New Balance already sources renewable electricity and Green-e certified Renewable Energy Certificates (RECs) that cover our US-based offices, distribution centers, and five footwear manufacturing facilities in Maine and Massachusetts, while rooftop solar provides approximately 30% of the electricity at our Flimby, U. factory. In June 2019, we marked a key milestone by generating a total of more than one million kilowatt hours in solar energy at Flimby. Located on the Solway coast, Flimby presents an excellent opportunity for wind power. We are currently investigating potential wind turbines that could provide enough energy to meet 100% of the factory demand through on-site generation.
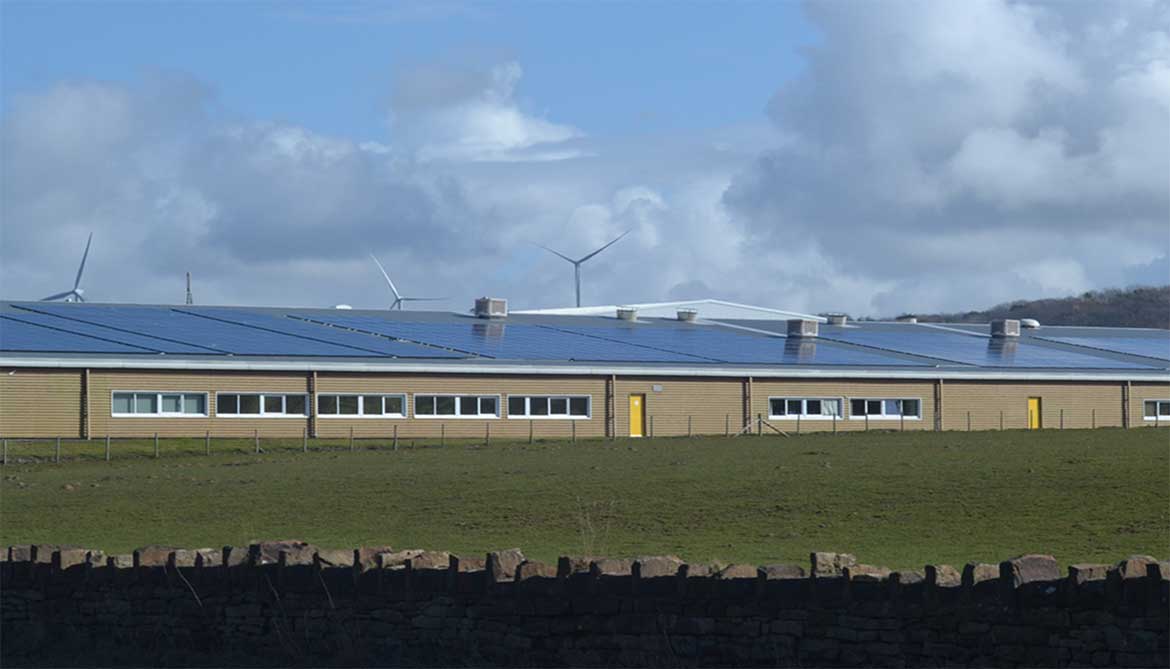
“New Balance has always believed that making things matters, but how they are made matters even more. By taking action across our own global operations, especially in our owned factories, we can demonstrate clear leadership as we pursue even wider adoption of renewables and other measures across our supply chain and industry,” says Joe Preston, New Balance president and CEO. “We recognize that addressing climate change requires innovation and new ways of doing business. We are excited to join with many of the world’s leading companies to amplify our voice, learn from those that have done so much already and help accelerate change at a larger scale.”
Beyond our own operations, New Balance is joining forces with the broader textile, apparel, and footwear industry to move toward a common commitment under the UN Fashion Industry Charter for Climate Action. This Charter encompasses our global footprint, including emissions associated with our global supply chain and the materials used to make our products. As a signatory, New Balance commits to a 30% reduction in greenhouse gas emissions by 2030. Key steps to accomplish this will be prioritizing materials with low climate impact, eliminating new coal and promoting renewable energy across our supply chain, supporting more circular business models, and engaging in closer dialogue with consumers to increase awareness and change behavior.
-
Renewable energy in our supply chain is still emerging, but we are seeing positive developments:
- One of our apparel suppliers in Sri Lanka, Bodyline (Pvt.) Ltd., an affiliate of MAS Group of Companies, is striving to become net positive and aims to use 100% renewable energy by 2025.
Bodyline has already started implementing large-scale solar photovoltaic (PV) systems and is investing heavily in renewable energy sources. - In Vietnam, we are working with V-LEEP to help steer government policy that can improve access to renewables, and we continue to engage with the International Finance Corporation (IFC) to assess feasibility of rooftop solar at several footwear supplier sites.
According to the World Economic Forum (WEF), water quality and availability is one of the biggest threats facing the planet over the next decade.* New Balance is committed to working with our suppliers to better understand and manage water impacts throughout our supply chain. Collectively, we need to use less, and we need to ensure that the water we do use is clean when discharged back into the environment.
Leather tanning and textile manufacturing (particularly the dyeing and finishing of fabrics) are often very water- and energy-intensive. In 2016, we began assessing water-related risks at our most important material suppliers, as well as measuring water use and establishing more stringent wastewater discharge requirements.
Consumption Volume
We began collecting water data from strategic tanneries and textile mills in 2016 to assess water use and wastewater discharge. Fifteen suppliers reported water consumption rates higher than 500m3/day. In 2018 and beyond, we will continue to collect this data and more broadly benchmark supplier performance using Higg FEM v3.0, ZDHC Wastewater Guidelines, and data available within the Leather Working Group audits for tanneries.
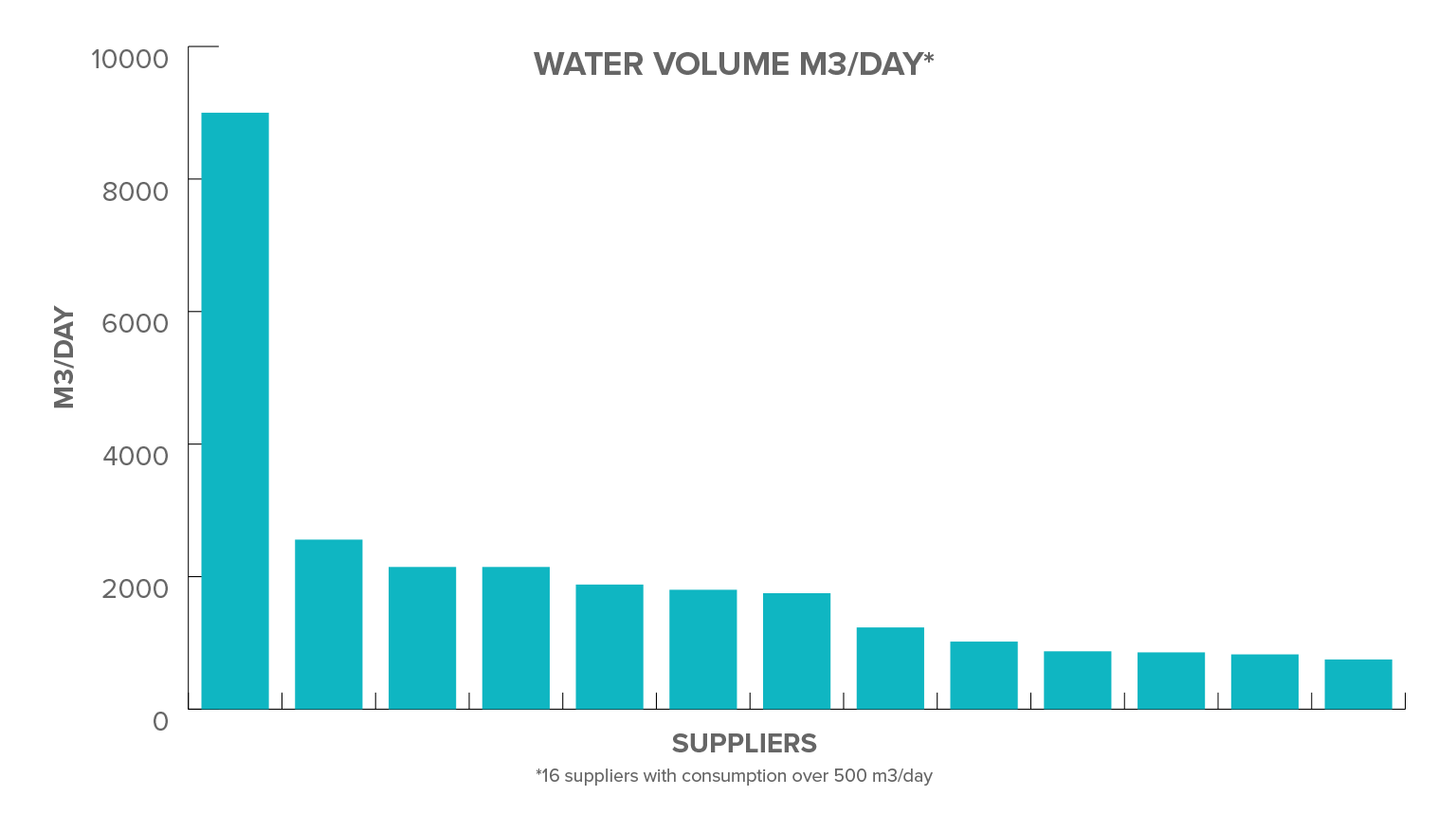
Location Risk
In 2016, we mapped 30 of our top Tier Two supplier locations using The Water Risk Filter maps from the World Wildlife Foundation (WWF) to identify regions where water stress and flooding have the potential to impact our supply chain.
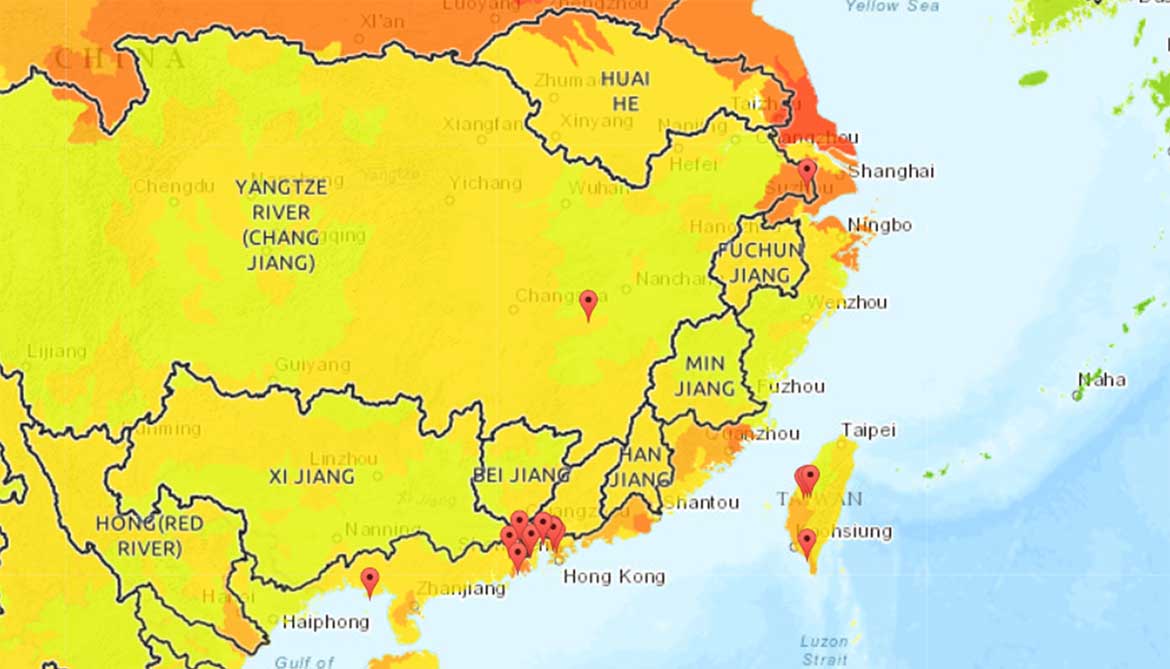
Wastewater Violations
In China, we use the Blue Map Database, developed by the Institute of Public & Environmental Affairs (IPE), to screen all supplier facilities for any known wastewater violation records for Tier One and Tier Two facilities.
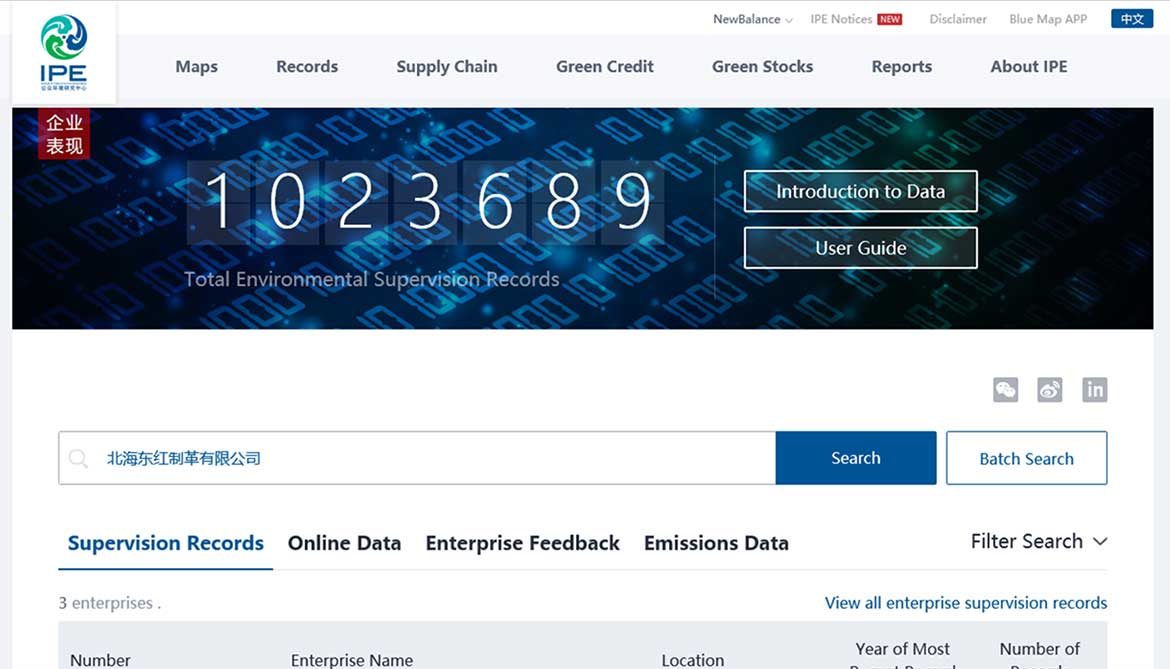
Together, these three assessment tools paint a picture of where and how we are addressing water risks. For example, any supplier with a violation is required to go through a formal “delisting” process with IPE to demonstrate the issue has been resolved through a corrective action review and monitoring, done by IPE. Delisting must be completed within six months, and any new suppliers must resolve their issues before any orders can be placed.
In the first quarter of 2018, we screened a total of 218 active suppliers in China and uncovered 11 violations (two within Tier One and nine within Tier Two). One supplier has already taken action and been delisted, three are in process of providing feedback to IPE, and we are actively working with the remaining suppliers.
ZDHC WASTEWATER GUIDELINE
In April 2013, New Balance joined the Zero Discharge of Hazardous Chemicals (ZDHC) Roadmap to Zero Programme – a coalition of major apparel and footwear brands and retailers that are committed to leading the industry towards zero discharge of the industry’s most hazardous chemicals. ZDHC has put forth a Roadmap that demonstrates the collaborative efforts of the organization and how ZDHC contributors intend to lead the apparel and footwear industry towards better chemical management.
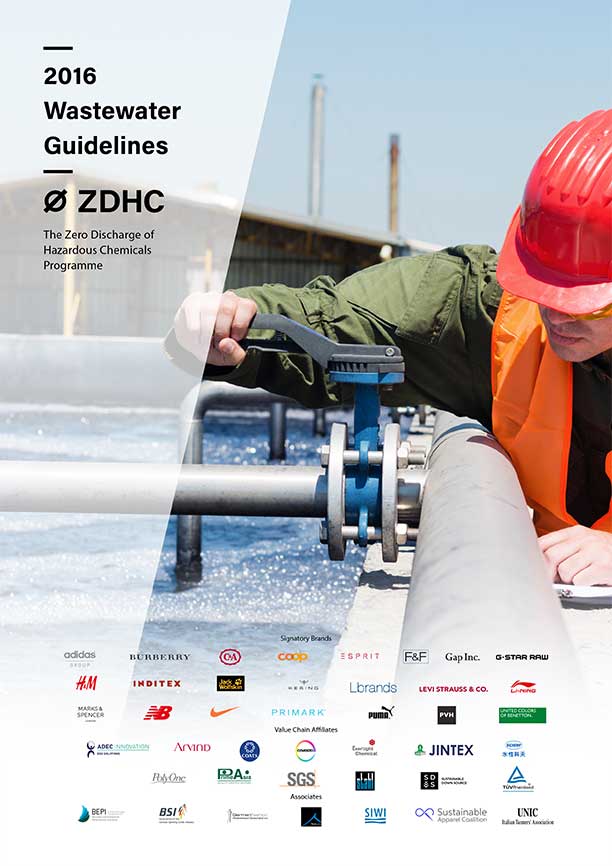
New Balance played a leading role in the development of the ZDHC Wastewater Guidelines, which the organization launched in 2017 to serve as a progressive industry standard to replace the duplicative and conflicting wastewater standards of the past.
New Balance adopted the ZDHC Wastewater Guidelines in 2017 and has begun rolling it out to our supply chain. We began testing against the Guidelines in 2017 with a group of our largest suppliers. The next round of testing is due in April 2018. Our participating Tier Two suppliers will be expected to meet “Foundational” performance by the end of 2018, and then increase to “Aspirational” by 2020 per the overall ZDHC goals.
We will continue to assess risks, identify next steps and determine how to best engage with suppliers to improve water stewardship. Ultimately, we will be looking for our suppliers to use less freshwater, improve water reuse, and return wastewater to the environment cleaner than required by local, national and international standards.
PARTNERSHIP PROGRAM: NRDC Clean by Design
NEW BALANCE SUPPLIER: Far Eastern Dyeing & Finishing Ltd. (apparel textile mill)
LOCATION: Suzhou, China
REASON: High-risk location, high water usage/day
OUTCOMES: Wastewater discharge reduced by almost 1.3 million m3, and 1,058 tons of coal equivalent (TCE) saved (4.7 million RMB, or 740,000 USD)
Recent work with one of our strategic textile mills highlights the importance of evaluating and addressing environmental risks with Tier Two materials suppliers.
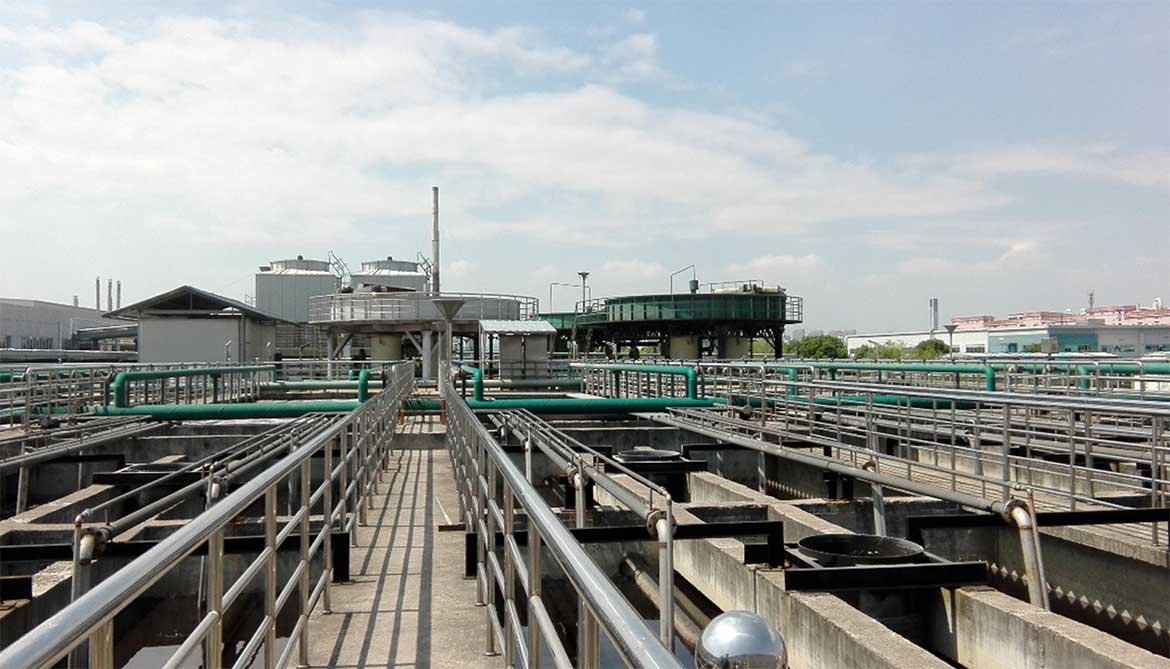
In 2015, we urged one of our largest textile suppliers to join the Natural Resources Defense Council (NRDC)’s Clean by Design program to undergo extensive water and energy efficiency evaluation and planning. The results were significant.
It is important to note that Far Eastern is not a problematic supplier. In fact, it is quite sophisticated and has been engaged on environmental work with other brands in the past. New Balance represents only a small portion of its total business. However, the importance of Far Eastern lies in its scale: the entire Far Eastern site uses almost the same amount of energy as New Balance’s entire Tier One footwear manufacturing base. As such, with its successful participation in the Clean by Design program, Far Eastern was able to generate energy savings in excess of 1,000 TCE, which is roughly equivalent to the entire energy usage of a small- to medium-sized footwear manufacturing facility.